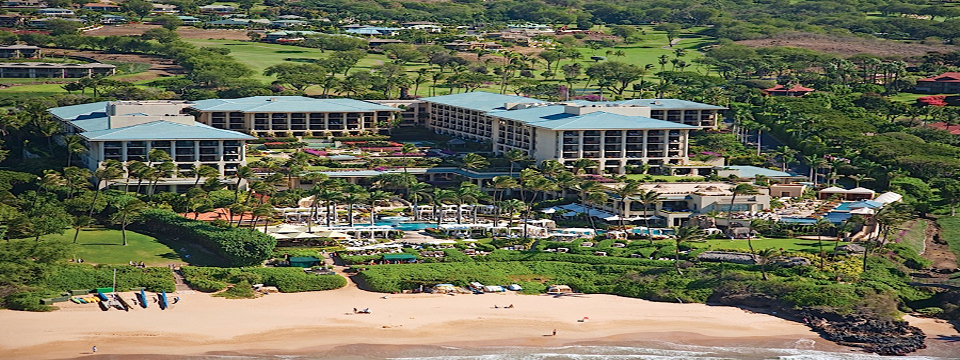
Challenge
Priding itself on the exceptional luxury it provides, Four Seasons Resort Maui needed to replace its aging, unreliable mechanical equipment in order to maintain a high level of comfort for guests. The resort also desired to improve the efficiency of its systems to combat the high utility costs on Hawaii’s outer islands. Four Seasons sought an established service and maintenance partner to support the upgrade of its aging systems with new chillers and heat pumps. In keeping with its commitment to comfort, it was important not to disturb guests during construction.
Solution
Providing reliable comfort
Four Seasons’ engineering consultants, Michael Hattori and Assoc., along with mechanical contractor, Dorvin D. Leis, and equipment and controls consultant, Trane®, initiated a three-phase design build project. Piping was engineered to transition from constant to variable volume chilled water flow. With a “long barrel” evaporator design, considered complementary to variable flow conditions, three Trane 350-ton CenTraVac™ water-cooled centrifugal chillers were selected. The chillers are capable of sustaining operating temperatures down to 34°F and offer full-load efficiency levels averaging 15 percent better than competitive chillers. With one moving part and low-speed operation, CenTraVac chillers provide reliable operation for continuous comfort.
Improving efficiency, reducing costs
The chillers were arranged in a variable primary flow control sequence, allowing chilled water flow to vary throughout the system. With fewer pumps, motors and wiring, as well as less piping and labor, the system reduced Four Seasons’ installation costs, lowered operating costs and improved reliability. The water-cooled centrifugal chillers are equipped with Trane Adaptive Frequency™ Drive (AFD) technology. The AFD maximizes chiller efficiency and reduces power consumption by adapting the compressor motor speed and inlet guide vanes to the chiller operating load, reducing electricity consumption and cost of chiller operation.
Optimizing performance
To satisfy hot water demand, two state-of-the-art modular, scroll compressor heat pumps replaced the resort’s aging equipment, along with an entirely new hot water system. The heat recovery heat pumps stage the number of running compressors as a function of the heat pump condenser water inlet temperature.
The heat recovery equipment works in concert with an 8,750 gallon heat recovery storage tank. The equipment captures heat from the laundry’s flash steam, helping to meet peak hot water demand. Domestic hot water generated by the water-to-water heat pumps draws upon chiller condenser water returning from the cooling towers, using it as a heat source in place of chilled water return, to increase the effectiveness of the heat pumps, as well as provide a lower condenser water temperature for the chillers. The lower water temperature provides significant chiller savings when more humid air raises wet bulb temperatures.
In phase three, variable frequency drives were installed on air handling units with motors greater than 5 hp. Temperature control strategies for the HVAC units, using a combination of supply air reset and volume control through variable fan speed, are designed to work in conjunction with variable chilled water flow to maintain the difference between chilled water supply and return close to chiller design conditions.
Maximizing energy savings
A Trane® Tracer Summit™ building automation system (BAS) monitors and controls the central plant by coordinating lead and lag chillers according to load and optimum performance; cooling towers using wet bulb temperature sensing for qualifying set point; and HVAC air handler and exhaust fan run times and speeds according to building needs. The heat pumps are integrated with the heat recovery system to enable use of thermal storage, releasing heat energy during times of peak demand that further reduces building electrical demand.
Results
Trane CenTraVac™ water-cooled centrifugal chillers, an entirely new domestic hot water system, and Trane controls were designed and integrated to support the efficient operation of the central chiller plant at the Four Seasons Maui Resort. Early results are encouraging with the chillers providing chilled water at approximately 0.42 kW per ton and the entire plant, inclusive of pumping energy and cooling towers, returning approximately 0.55 kW per ton. The optimized central plant operation, complemented by the Tracer Summit control system, has reduced the building’s annual kWh consumption by 20 percent (equal to 2,400,000 kWh per year), mirrored by a 20 percent or 400 kW reduction in maximum demand.