Summer Energy Best Practices
July 24, 2018
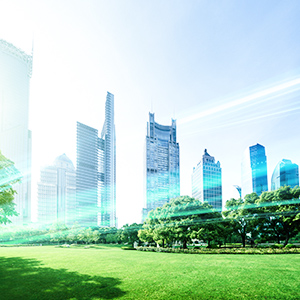
In the warm summer months, electrical demand goes up, driving prices higher. Meanwhile, HVAC equipment kicks into high gear to keep occupants cool. It’s the annual conundrum as building operators struggle to maintain the balance between cost and comfort. It’s time to take on a few summer energy projects.
Know the goals. Target what’s most important to the organization: reducing energy use, lowering demand at peak rates, improving system operation, or decreasing comfort calls.
Define the metrics. Measure to prove progress: compare past and present energy bills, or use data and reports from the building automation system.
Take action. Where to begin? At Trane, we’ve narrowed it down to three best practices that, combined, may deliver 10% to 25% in energy savings* for our customers.
Strategy 1: Review system scheduling and setpoints
In its simplest terms, system scheduling involves setting the temperature up or down according to building occupancy schedules. Today this is not as straightforward as scheduling to an 8 to 5 work day. Flex time, work-from-home and summer hours bring much more variability to building occupancy rates. And with fewer human bodies in the building using heat-generating computers and other equipment, you may be able to reduce HVAC system operation. Check with department managers or HR to find how many people are actually in the building at any given time to ensure that you’re not wastefully running HVAC systems for full occupancy.
How cool is comfortable? Many commercial buildings are notoriously over-cooled. It should go without saying that if people are huddled in sweaters during August, you can safely raise the thermostat set-point a degree or two, or move sensors around to get better readings—a sensor placed in direct sunlight may give an inaccurate reading for a large open workspace.
Strategy 2: Shift energy demand
While you’re reviewing scheduling and set-points, look for ways to shift energy use to off-peak hours. Along with the obvious immediate savings, some utility companies actually base the entire upcoming year’s electricity rates on a narrow timeframe of peak demand use. Incidentally, peak demand is defined by the utility company and it isn’t necessarily in the middle of the 9 to 5 weekday. In some regions, particularly where solar energy use is strong, new peaks have been established during the evening and nighttime hours.
How do you know when your building uses the most energy? Utility bills typically provide some information. We also use an energy visualization tool that creates a picture of hour-by-hour energy use. Once you know when the building is using energy, it is easier to figure out why. Then you can collaborate with other managers to shift energy-intensive operations to off-peak hours. Or, if you can’t change when equipment is used, you may be able to change when the energy is created. For example, you can implement thermal (ice) storage to freeze ice at night to cool the building during the day.
Strategy 3: Continuous commissioning or re-commissioning
As summer goes on, it’s a good idea to give the HVAC system an overall review and restore it to the original performance standards. A few minor flaws may not seem like a big deal, but when the system is working hard and energy costs are high, the little anomalies end up costing a lot.
Here’s what to look for:
- Manual overrides keeping settings out of spec
- Outdated or poorly located sensors in reconfigured spaces
- Valves and dampers that are stuck open, causing the endless cooling of hot, humid air
Check the system every few months, at least. If you’re still operating in manual mode, that can mean a clipboard check of every thermostat, sensor and piece of equipment. The process can be much more streamlined in connected buildings that can detect system flaws in the data on a continuous basis.
Start small. Focus on continuous improvement.
Time and budget constraints are the barriers to progress. But doing everything at once or doing nothing at all are not the only options. Starting with small energy projects and ECMs can be the perfect solution. By recognizing strategies for identifying, prioritizing and validating ECMs, you can start with the most beneficial projects, build momentum for future energy projects, and ultimately develop a measurable continuous improvement plan.
Managing energy supply and demand can be extremely complex. There is a wide array of energy services available today, spanning virtually every aspect of energy use. We can help fill in the gaps if your team needs help.
*Savings based on national Trane project averages, variations in energy cost, geography and project scope will impact exact savings actualized for each customer.