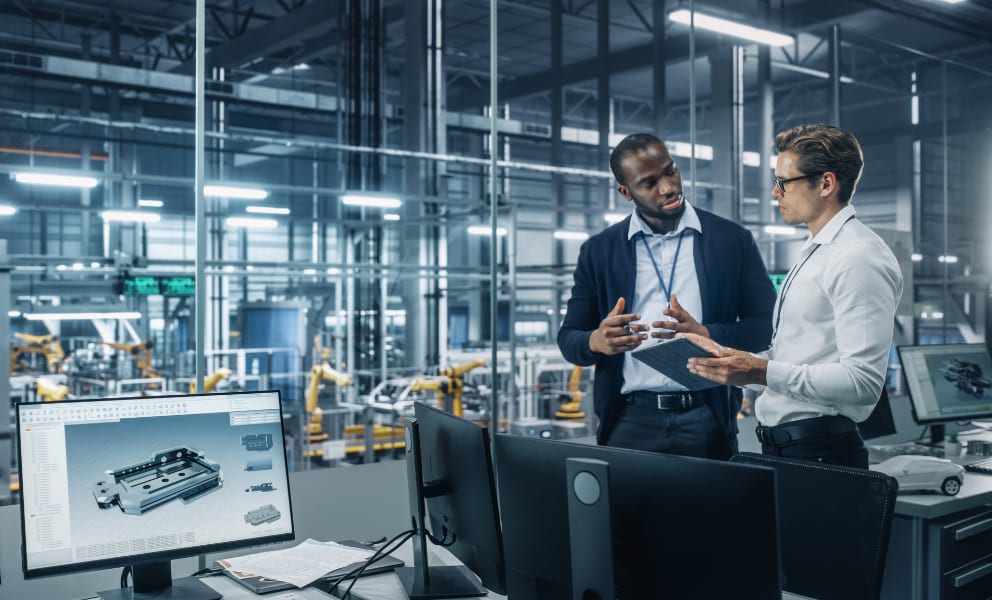
Beyond managing comfort.
Commercial cooling systems keep the spaces where we work, play, dine, shop and live at a comfortable temperature no matter how hot it gets outside. In the manufacturing world, cooling must address the complexities of managing ambient conditions for industrial processes – think data centers, chip manufacturers, electric vehicle ecosystems, food and beverage manufacturers or life sciences companies. For these applications, parameters are much more stringent. In addition to maintaining a steady indoor environment to ensure process output is consistent, protecting the health of workers is mission critical.
With lots of latent heat, ventilation and space cooling is paramount to not only keeping workers comfortable but safe. The risk of “getting it wrong” has consequences far more severe than a room that is too hot or too cold.
Manufacturers ranging from start-ups to Fortune 500 companies, and everything in-between utilize process cooling systems to support operations that are core to their organizations.
What do process cooling users care about?
While the degree and intensity of concern about process cooling depend on the nature of the application, industry requirements, environmental conditions and other factors, many customers who buy and use these systems care about several key things:
- Reliability – Is the system designed with product performance and reliability as top priority? Does it perform reliably and with minimal downtime? How quickly and effectively can it be serviced when required? Are maintenance services available and reliable? Is the supply chain for parts and services diversified and secure?
- Costs – These systems are not inexpensive, so will they run efficiently, minimize the opportunity cost of downtime and produce energy cost savings? Is cost modeling available to help predict energy costs? Are preventative maintenance schedules available to avoid repair and downtime costs and suggest the best maintenance plan? Are predictive analytics available to help save money and time, and improve productivity?
- Support of business needs – How knowledgeable is the manufacturer from an industry and domain perspective? Are they active in ASHRAE® and well-versed in LEED, Energy Star and other industry standards? Does the manufacturer offer a broad range of products or are they focused on only a few? Are the products designed with Industry 4.0 compatibility in mind? Where are service technicians and spare parts depots located? Can the manufacturer support global projects and systems? Are the systems operationally secure?
- Meeting sustainability and cultural goals – Are systems and products designed with sustainability principles in mind? How does decarbonization factor into the manufacturers’ products and services? How energy-efficient are the products? Are the systems designed to conserve water? Does the organization invest in workforce development, safety, diversity, inclusion, and equity initiatives to create an inclusive culture for all?
Managing risk along all these dimensions.
Given all these considerations, how can organizations reduce their risk? The opportunity cost of unplanned downtime can be devastating. Whether a cooling unit is down for a day or for a week can have enormous consequences: lost revenues, damaged product or inventories, lower employee satisfaction, slower speed to market and more. For example, if a chiller goes down for one day that might mean $1 million in lost revenues. But if that chiller can’t be serviced for four days, the lost revenue is significantly greater—to the tune of $4 million.
In the Life Sciences world, when COVID-19 erupted, vaccine makers needed to ramp up their development and scale manufacturing processes to be first to the market and increase revenues more quickly. To do so, they needed to have complete reliability in their equipment.
Semiconductor companies are in a race to build chip fabrication capacity and win market share; they need reliable, industry-leading HVAC equipment delivered on time, from a trusted partner.
Electric vehicle manufacturers are also in stiff competition to gain market share and help the environment. They cannot afford to have processes and systems that are rigid, inflexible, unreliable and slow. Likewise, food and beverage manufacturers must have constant precision monitoring of their environments and operations to avoid product contamination and costly recalls.
All these industries rely on effective and efficient process cooling in their manufacturing facilities. As they look to mitigate risk in all facets of their operations, predictive analytics, connected services and remote maintenance can be used to maximize uptime more effectively. Early detection of issues and remote mediation offer a promise of “downtime on YOUR time,” rather than reactively responding to unforeseen emergencies.
Predictive analytics can also help drive planned maintenance events that are cost-effective, less frequent and shorter in duration. Remote monitoring and diagnostics use digital twins of equipment to help spot potential failures faster so critical parts can be on hand to avoid costly downtime. Manufacturers with equipment rental or leasing capabilities in multiple locations can also step in with solutions that accelerate deployment or keep operations going if issues occur.
Let’s have a conversation.
Trane offers all these capabilities: high production quality in producing equipment that is reliable and durable; systems customization and applications expertise; a global footprint and highly responsive service model; focus on intelligent services to minimize costs, including predictive cost modeling; industry and domain expertise; and services related to meeting sustainability needs. To start a conversation about your process cooling needs, contact a Trane expert today.