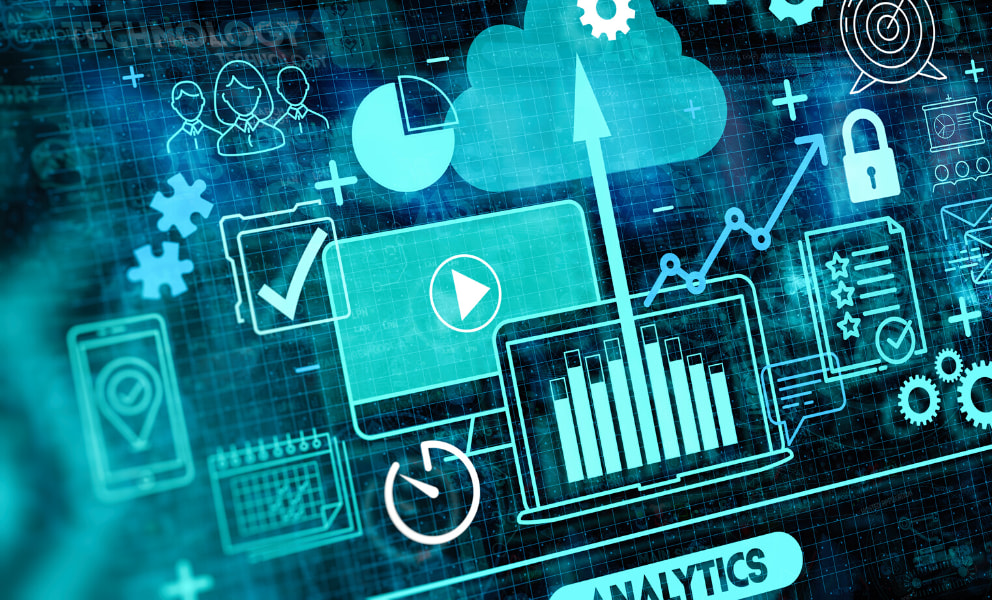
Industry 4.0 is here and is dramatically changing how industrial facilities are managed. Just as our watches have evolved from telling time and counting steps to sending text messages, measuring our heart rate and exercise and providing weather updates, building maintenance and management has evolved significantly as well. New products and technologies are being integrated into production facilities and throughout building operations.
With many industries facing wholesale change across most facets of their operations, leading organizations do not only want to but also know they MUST transform to stay relevant. And they must do so with urgency. However, they often find their transformation to Industry 4.0 is slower than expected and doesn’t always yield the desired results.
For companies in the Life Sciences sector, laser-tight control of the physical environment is paramount to producing products that will be accepted by regulatory bodies—in pharmaceuticals if the ambient conditions during drug manufacturing are not tightly controlled the entire product may have to be thrown out. Connected, cloud-based control of critical equipment allows manufacturers to keep the necessary watch for early indicators that the ambient temperature could be impacted.
In high-tech sectors such as semiconductor or electric vehicle manufacturing, who run massive manufacturing operations, digital and cloud technologies are a huge competitive advantage in keeping plants operating 24/7 which enables the scale necessary to get products to market, first—a mainstay of their existence.
To respond to these changes, leading companies that have been successful in leveraging Industry 4.0 to realize faster and more sustainable transformation are leveraging digital technology to build more agile and customer-focused organizations. This approach lets manufacturers focus on improving their productivity, sustainability, agility, speed to market, customization and customer satisfaction—all of which can lead to tangible increases in revenue. How so?
1. Connected controls mean better insights and improved decision-making capabilities
Many parts of a manufacturing facility can be measured: temperature, occupancy, energy use, equipment inefficiencies. Connected and integrated sensors throughout a facility can detect subtle variations such as change in relative humidity and call for the system controls to adjust the ambient conditions without sacrificing efficiency or risking a deviation from tightly managed set points.
If Indoor Air Quality (IAQ) is of concern, sensors throughout a facility can indicate whether a space is occupied and serve the right amount of outdoor air to increase air flow. Industries can now leverage cloud-based technologies that enable secure remote access to critical systems and processes, and make system monitoring more immediate, so decisions can be made quickly to solve issues.
With connection points in all parts of a facility, data on run-time, component health, power usage, and more can be analyzed to help improve the efficiency of the HVAC equipment, bolster energy efficiency, cut costs and meet sustainability goals.
2. Predictive services using data, analytics, artificial intelligence (AI) and machine learning (ML) help identify issues early
A recent publication by McKinsey & Co estimates that Industry 4.0 can unlock significant value across multiple areas of a factory network. For machine downtime alone, a 30-50% reduction may be realized. And improvement in forecasting accuracy can be as much as 85%.1
Using data and analytics that maximize human-machine interactions by leveraging artificial intelligence (AI), automation tools, and Machine Learning (ML) can help identify operational issues before they arise and help avoid costly downtime. For example, measuring the internal temperature of the bearings inside a chiller unit can indicate whether a chiller is in good health or whether imminent maintenance will be necessary.
Predictive analytics can also help drive planned maintenance events that are cheaper, less frequent and shorter in duration.
Connectivity combined with data, computational power and advanced analytics can create value throughout the production value chain.
3. Digital technologies—like the use of digital twins—enable scenario modeling and help predict product lifecycle or needed maintenance
Digital technologies, such as the use of digital twins to mirror a process or facility, provide the ability to analyze many operating variables at once and then model ‘What-if’ scenarios that can help predict vulnerabilities in a process, run-time errors, equipment stress and more. Remote monitoring and diagnostics that use digital twins also help spot potential failures faster so critical spare parts can be on hand to avoid costly downtime.
Essentially, with digital twins, teams can focus on solving problems that move an organization ahead versus spending time on the manual manipulation of data.
Let’s talk about your transformation needs
Trane can guide you through a digital transformation to Industry 4.0 that can help to improve uptime, increase reliability, reduce costs and help meet decarbonization and sustainability goals. We take a holistic approach to helping you manage your journey. Our Wayform approach combines the trusted advice of Trane professionals with building data and insights to help industrial manufacturers use energy more intelligently and reduce carbon emissions. We work with our clients throughout the entire planning, implementation and ongoing servicing process. We produce durable, high-quality equipment; offer systems customization and applications expertise; focus on intelligent services to minimize costs; and provide deep industry and domain expertise. Let’s start a conversation.
1 Capturing the true value of Industry 4.0, April 13, 2022, McKinsey & Co