Designing an HVAC System When Your Building Occupants are Green
November 15, 2019
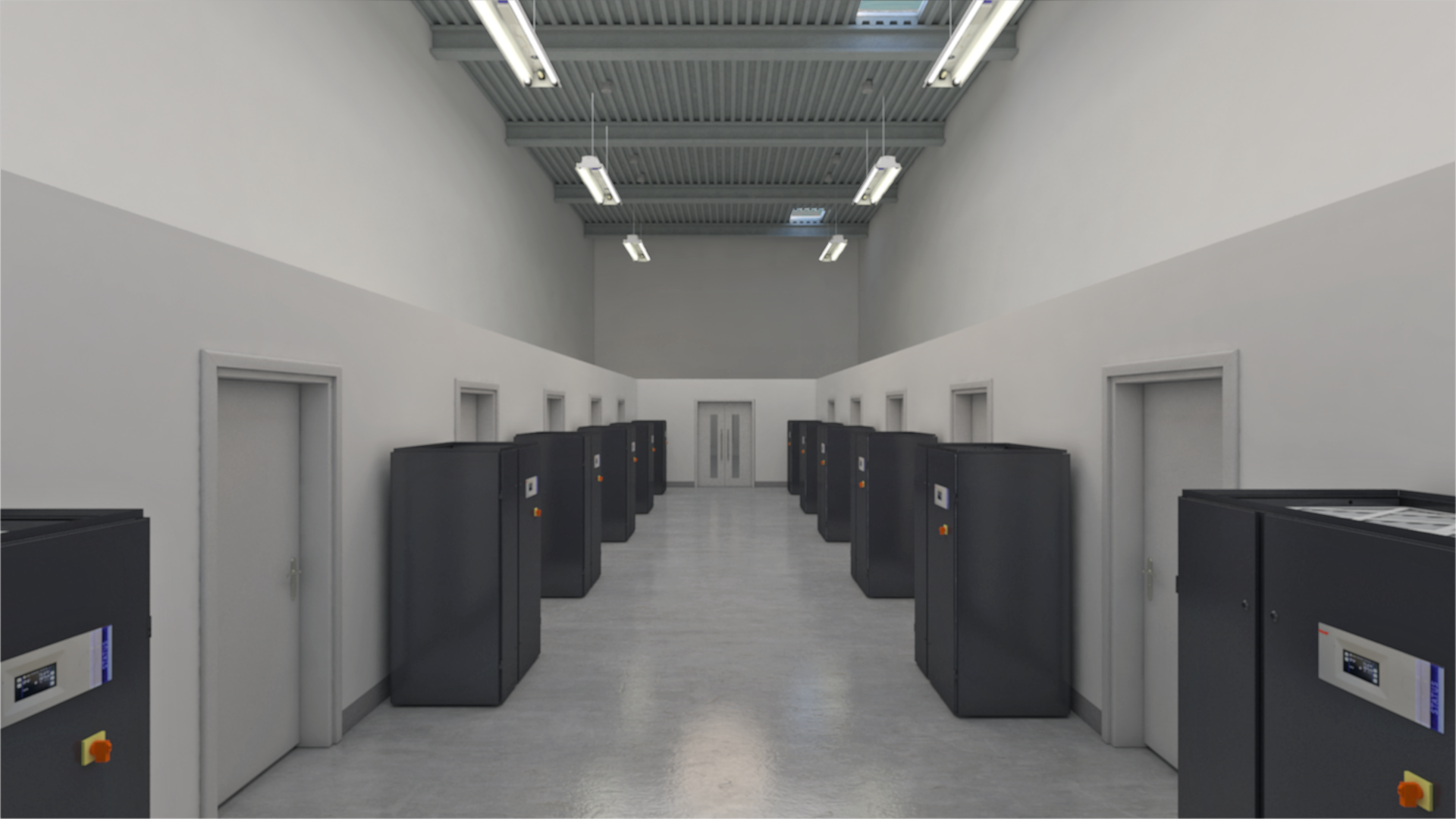
Green plants, such as lettuce, cannabis, kale, basil, and other crops, are being grown by indoor agriculture producers around the world. The industry is growing rapidly for a variety of reasons. The ability to grow fresh foods, year round, in areas where harsh winters or scorching desert heat prohibit planting outside, is one of the compelling reasons to bring crops indoors. With indoor agriculture, foods can also be grown locally, which shortens transport time, helping to increase freshness and reduce spoilage. And while it might sound like a simple solution to solve some of the world’s food production issues, indoor agriculture isn’t without its challenges. Maintaining an optimal environment is just as important when plants are grown indoors as when they are outside.
Zoning in on specific needs and functions
All plants have basic needs including nutrients, minerals, vitamins, water, oxygen, and carbon dioxide (CO2). With these needs satisfied and the right temperature, humidity and lighting conditions, plants can thrive. But some plants need even more stringent control of artificial light to enable them to mature, fruit and seed properly. Others specify a tight temperature tolerance in order to flourish. While optimal conditions can vary from plant to plant, just as they do for human occupants, the indoor agriculture building might require multiple zones to accommodate the growing of different crops, and conducting varied functions such as drying, curing, trimming, and processing.
The difference is night and day
Traditional buildings generally operate in occupied/unoccupied modes. However, green occupants are there 24/7/365, and require their needs be met for both lights on/“daytime” and lights off/“nighttime” modes. Cooling and dehumidification are critical when the lights are on. When the lights are off, the primary need is dehumidification, and possibly heating if the plants are expected to add a significant cooling load.
When the process runs hot and cold
When designing the HVAC system, calculations should consider both sensible and latent loads. The lighting densities, especially when simulating “daytime”, can be much more intense than you would find in a comfort cooling building. A traditional building requires 0.7 – 1.2 W/ft2, while an indoor agriculture facility require 30-80 W/ft2. This intense “daytime” lighting, along with the water pumps, air transfer fans and other equipment used in the plant growing process result in a high sensible load. In the “nighttime” mode there is little sensible load, but some latent load from evapotranspiration (water movement from soil and plant to surrounding air), infiltration and additional moisture-generating processes. As the plants evaporate water, sensible cooling occurs, which results in a space cooling load.
Plant preferences redefine performance points
Building temperature and humidity requirements also differ between a comfort building and an indoor agriculture facility. Traditional occupants are generally comfortable with temperatures between 70 and 75 degrees Fahrenheit, and relative humidity ranging from 50 to 60 percent. However, plants thrive in a broader temperature range, between 65 and 83 degrees Fahrenheit, and relative humidity levels from 40 to 75 percent, depending on the type of plant. In addition, plants are continually adding moisture to the air, which affects humidity levels and makes dehumidification a critical element of the indoor agriculture HVAC design.
Ventilation is also important for human comfort, and for most buildings it is based on ASHRAE® Standard 62.1 Requirements. Indoor agriculture environments, however, often require no ventilation. In fact, with plants consuming CO2, many growers desire to increase the CO2 beyond ambient conditions, choosing to recirculate the air rather than ventilating, which can dilute the CO2.
Solutions from simple to sophisticated
In order for plants to thrive, it is critical for indoor agriculture building designers to ensure the HVAC equipment can effectively cool, heat and dehumidify the space where crops will be grown. But just like when designing an HVAC system to handle traditional comfort needs, with an indoor agriculture facility, one solution doesn’t fit all.
Budget, operating cost, control requirements, and data capabilities are important considerations for an indoor agriculture building’s HVAC. A readily available, simple packaged or split direct expansion system works well for small, single-zone applications. For larger spaces, a purpose-built DX unit can handle both sensible and latent loads with improved energy efficiency. And for more sophisticated operations, an applied chilled-water and air-handling unit can prevent air from zone 1 mixing with air from zone 2, while offering flexibility, opportunities for waterside free cooling and heat recovery, higher efficiency and a longer life expectancy. It’s important to note that when designing an HVAC system for indoor agriculture, special consideration of the unique requirements of the operation can maximize production, build long-term ROI, and help the business and its green building occupants thrive.
Want to learn more? Visit trane.com/indoorag