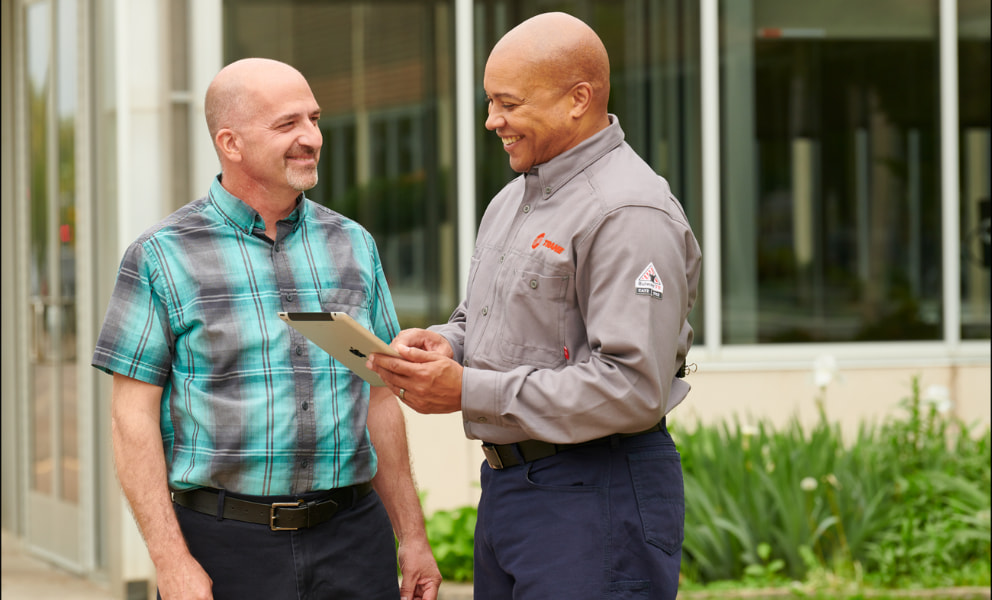
Planning for the Worst to Deliver Your Best
No one wants their HVAC unit to go down, but in a manufacturing plant the cost of downtime can add up—and quickly. More than likely, you have redundancies in place for your critical process equipment. If a machine goes down, you and your staff are prepared for a seamless transition. Perhaps you keep an inventory of key parts and have a technician on 24/7 call.
But what happens if your HVAC equipment has an issue? Do you have a plan for how you can maintain your ambient or process conditions if a key chiller were to fail? Your process equipment and your product require precise control of the temperature, humidity and air flow in your space – knowing what you’d do if your HVAC equipment went down is just as important is planning for the worst-case scenarios in your own equipment.
With the challenges of today’s supply chain and industry conditions, it may be time to take a fresh look at how your contingency plans can remain relevant in the ever-evolving environment. How far does your plan take you beyond just fixing things when they go wrong? Are critical failures more preventable than you might think? Do your technical advisors venture deep enough into the possible issues you face and the best solutions to put in place? If not, it may be time for a new technical partner.
So, what should today’s contingency planning include? Here are a few considerations:
Scalability matters
Being able to scale operations quickly—to produce more product and be first to market—is critical and represents a huge competitive advantage. Using temporary rental equipment during the scale-up can be an invaluable solution to get equipment in place quickly and expedite operations. It also allows you to test processes with proof of concepts—to make sure processes will work—before making a large capital investment in equipment. As an organization moves a production line from small to large, or a new product requires condition or process tweaks, this approach enables manufacturers to start building a new product in situ to get the ideal long-term design just right.
Uptime is king
It’s as simple as this: if your equipment is up and running, you are capitalizing on your investment, and if it isn’t, you’re losing dollars for every minute or hour of downtime. Ensuring that you have reliability in your equipment and environment will avoid this loss of revenue, especially if you are running high-dollar processes. In the high-tech industries such as micro-chip and electric vehicle (EV) manufacturing, who have massive-scale productions, every minute of downtime represents significant money and productivity lost. The goal: always be on and working around the clock.
Ideally, your contingency plans include strategies for preventive maintenance, so crises are avoided altogether. Digital controls that provide real-time data should be in place to help monitor the health of equipment throughout your facilities, and predictive maintenance can help spot problems early to pre-empt major issues. If you know a piece of equipment is likely to fail in July, for example, you can schedule minor maintenance in May and avoid unplanned downtime to fix a major issue later. This is “downtime on your time.”
Rental equipment can also be used as a temporary solution when unforeseen issues arise. Working with a rental company that knows your business and can get equipment and parts to the place of need at speed is critical.
Build in redundancy
Owners of large manufacturing processes also use rental equipment as a means of preventing major failures that would shut a process down altogether. If there’s a critical failure on HVAC equipment, for example, a redundant chiller could be on standby or already in place to offer a quick cutover that would ensure operations continuity and minimal downtime. A good HVAC provider can help forecast when you need redundancy for the entire year, or just for specific points in time—such as for critical production windows or the hottest months where design conditions are met or exceeded.
Let’s start a conversation
Many factors will affect your contingency plans, and it’s important to have plans that are updated for current market conditions, technological advances and new industry best practices. Trane is a trusted advisor who can help you plan for the entire lifecycle of your equipment and facilities. In addition to our robust rental engineering and equipment offerings, we are with you on your journey to advise on all elements of your plan: equipment sales and ongoing service, controls and monitoring, predictive maintenance, data and analytics support, and our unmatched network of equipment and service providers. No matter where you are on your journey, let’s get started!