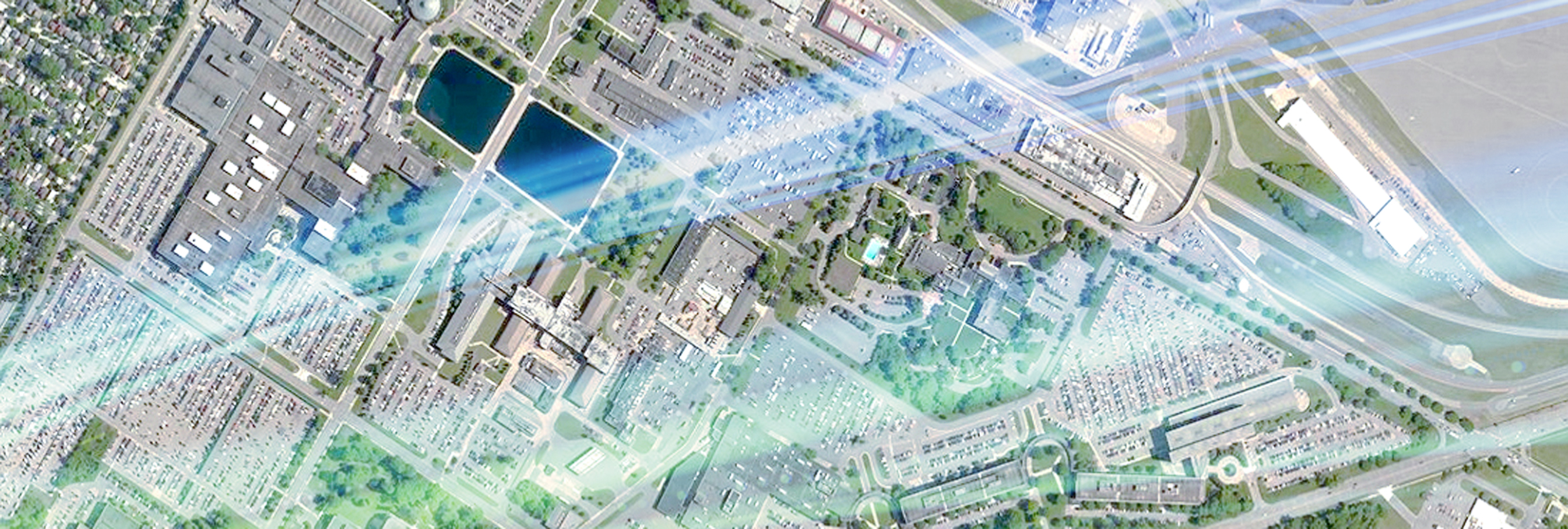
Challenge
Alignment with its climate change strategy to reduce global CO2 emissions and energy consumption were key considerations as Ford Motor Company initiated the transformation of its Dearborn campus to a modern, high-tech facility designed to foster innovation. As campus renovations were in progress, plans began to take shape for a large, Tier III data center that would be housed there. The data center would be one of two new facilities built to support an estimated 100 percent increase in the company’s data usage to align with the connectivity, manufacturing, and support of electric and driverless cars.
Data centers require substantial amounts of electric power for their IT equipment, as well as supporting infrastructure. It is estimated that cooling consumes ~40 percent of a data center’s power consumption, and is responsible for ~16 percent of its total operating costs. Ford sought to keep energy use and operating costs down as it outlined objectives for the 365 day a year/24 hour facility. The desired LEED® certifiable facility would incorporate a high-performance HVAC solution that would operate efficiently across all operational points. The critical nature of the data center dictated that the HVAC systems adhere to special tolerances and guaranteed chiller capacities to maximize uptime and lower total cost of ownership.
“As the Ford Motor Company transitions from an automobile company to a mobility company, we have a continually increasing need for more computing power,” said Dwayne Atkins, Ford Land Engineering Manager. “Construction of the new data center was in answer to that need. As we outlined project specifications, efficiency, sustainability, and the facility’s impact on global warming were all major factors.”
Solution
Ford evaluated its options as it selected an HVAC system partner for the new data center. Trane offered them a trusted relationship that spanned decades, and a single-point of responsibility for design, application engineering expertise, in-depth knowledge of energy saving technologies, and the ability to deliver reliable solutions for a mission critical application. Selected as the design build partner for the data center HVAC systems, Trane worked with Ford, the project’s general manager, mechanical contractor and engineers to develop premium solutions for the chiller plant design.
Providing a safe, sustainable solution with next generation, low GWP refrigerant
Six 670-ton Trane® CenTraVac® centrifugal chillers were selected to handle the cooling needs of the data center. Part of the Ingersoll Rand EcoWise™ portfolio of products designed to lower environmental impact, the chillers use low pressure refrigerants, which operate in a vacuum, virtually eliminating leaks and enabling near-zero emissions. CenTraVac chillers were the first centrifugal chillers in North America to operate with the next generation, low global warming potential (GWP) refrigerant, R-514A, with a GWP of less than two. The Trane centrifugal chillers are also the first commercial chillers in the world to earn product-specific Type III Environmental Product Declaration (EPD) registration, which proves the environmental claims regarding chiller performance and documents conformance with the stringent third-party certification requirements. “It was the Trane chiller’s use of R-514A refrigerant that was the key determining factor for our chiller selection,” said Mr. Atkins. “The refrigerant is stable, meets our greenhouse gas emissions and GWP criteria, and doesn’t pose any occupational or fire hazard risks.”
Ensuring efficient, quiet operation with minimal downtime
Ford witness tested the Trane CenTraVac chillers in operation at the Trane La Crosse, WI, plant to ensure they met all performance options and specifications before they were delivered and installed on the Dearborn Campus. The systems meet Ford’s KW specifications; and offer low power usage effectiveness (PUE) ratio and total cost of ownership. To further increase efficiency, when outdoor temperatures are cold, a free cooling option integrated in the design is used to chill water and can provide up to 45 percent of chiller capacity without running the compressor.
The CenTraVac chiller’s simple, rugged, design is reliable and requires little maintenance, helping to minimize downtime for the data center. Should there be a disruption, the chiller’s rapid restart capability quickly brings the system back online, ensuring that critical operations are not compromised. The chiller’s smaller footprint helps to optimize data center floor space and its low-speed, direct-drive design offers quiet, vibration-free operation, with sound levels below 80 decibels to meet UAW requirements.
“With the CenTraVac, you get a high-performance level without the complexity. The KW per ton was better and so was the overall operating cost,” said Mr. Atkins. “Plus, the quiet operation is world-class. During our initial walk through, I noticed some of our non-technical people putting their hands on the chillers to see if they were even running.”
Results
Ford Motor Company partnered with Trane to implement an energy efficient, sustainable and reliable chiller plant to ensure uninterrupted operation of the critical mission data center on its Dearborn campus. As a result, the company has reduced its energy use by 540,288 kWh per year and CO2 emissions by more than 330 metric tons. Annual operating cost savings are estimated at more than $35,000. Completion of upgrades that improve the bottom line, while simultaneously enhancing sustainability, demonstrates Ford’s outstanding commitment to environmental stewardship. The company has received numerous industry awards for the project.
Project Highlights
Challenge
- Mission critical application
- Alignment with climate change strategy
- Reduced energy use and CO2 emissions
- LEED certification
- Guaranteed chiller capacities and special tolerances to maximize uptime
- Lower cost of ownership
Solution
- Single point of responsibility supplier
- High-efficiency Trane® CenTraVac® chillers
- Low pressure, low GWP refrigerants
Results
- Energy use reduced 540,288 kWh/year
- CO2 emissions reduced 330+ metric tons
- Annual operating cost savings of more than $35,000
- Industry recognition
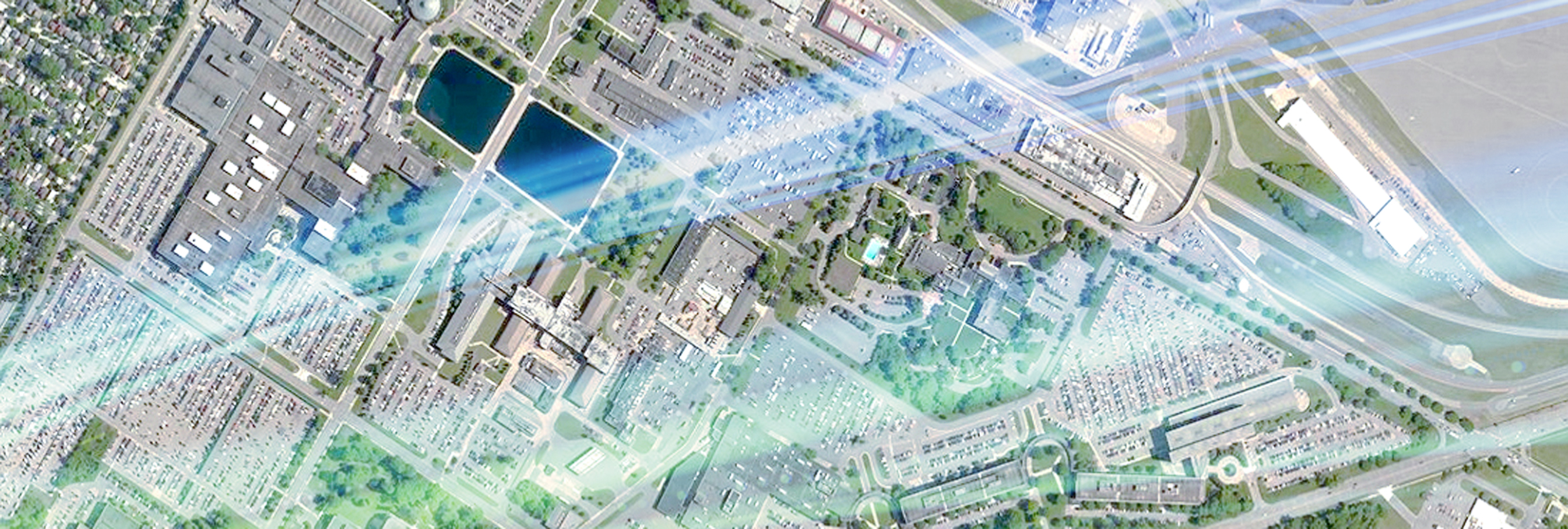