Summary
Constructed in 1982, the four-level, 171,870 sq ft, North Carolina Museum of Art (NCMA) includes offices, exhibit space and restaurant/catering operations. Each month, 25,000 visitors view the NCMA’s collection of treasures, worth in excess of $1 billion. The museum’s permanent collection spans more than 5,000 years, from ancient Egypt to the present, making the institution one of the premier art museums in the Southeast. Conservation experts and building operators are entrusted to work with the building and its systems to present and protect the collection for the citizens and visitors of North Carolina to enjoy now and for generations to come.
Challenge
The North Carolina Museum of Art was experiencing wide fluctuations in temperature and humidity levels, with swings of 30 percent humidity in the winter and up to 60 percent in the summer. What might have been a mere annoyance for another type of facility was a liability for the museum. Variations in climate could cause canvases to expand and contract, leading to premature aging, and hinder the museum’s ability to host national traveling art exhibits with strict environmental requirements.
Although facility managers knew the state’s budget did not afford the funds needed for system improvements, they also knew that without upgrades, the museum could potentially be an “artificial aging chamber” for its works of art. Besides preserving its treasures, the museum’s objectives included reducing its operational costs, energy use and greenhouse gas emissions, as part of a wider sustainability program.
Solution
Using the North Carolina PC bid process, NCMA requested upgrade proposals from several design/build suppliers. Based on the proposed savings, as well as the company’s creative approach and service track record, the North Carolina Department of Administration awarded Trane the state’s first capital improvement project funded by recently enacted performance contracting legislation and processes. Performance contracting allowed the government-owned facility operators to finance renovations and improvements based on guaranteed future utility and operational savings.
Controlling air flow and dew point
A modular Trane Climate Changer™ dedicated outside air handling unit was installed to pretreat, measure and control the airflow and dew point of the outside air entering the facility. The four existing constant volume air handlers were converted to variable air volume to reduce energy consumption. During unoccupied hours, a number of exhaust fans are cycled off and the airflow is reduced to account for the reduction in exhaust air from the building.
Centralizing humidity control
The dedicated outside air system uses one centralized high-pressure, high-purity, cold-fog humidification system, replacing ninety-two distributed steam humidifiers. The new system distributes the pretreated air to the main air-handling units at a constant 52°F dew point. With the need for boiler system steam humidification eliminated, the steam boilers were replaced with a hot water boiler system.
Top-to-bottom chilled water plant retrofit
The museum’s aging chillers and constant speed cooling towers were replaced with a variable speed chiller plant that includes two variable frequency drive Trane Earthwise™ CenTraVac™ centrifugal chillers. The chillers feature reduced evaporator and condenser flows and variable primary chilled water pumping, with more than 70 percent evaporator flow turndown. When outside air temperature is at or below 37°F, the chiller compressors are turned off and bypass valves in the chiller refrigerant circuit are opened to allow refrigerant to circulate without mechanical compression, satisfying 100 percent of the museum’s cooling load requirements.
Chiller tower optimization reduces energy use
Chiller and tower controls were upgraded from pneumatic controls to a direct digital control (DDC) system. The DDC system saves time by eliminating maintenance of air compressors and refrigerated air driers, and the need for chart recorders, data loggers and regular calibration.
Using a Tracer Summit® building automation system (BAS), museum facilities managers perform chiller tower optimization to minimize total energy use. This approach uses outdoor wet-bulb conditions in real time, as well as chiller loading, to calculate the optimal cooling tower set point.
Results
Backed by a Trane performance contract guarantee, the North Carolina Museum of Art was able to finance a complete retrofit of its heating and cooling central plants, air handling and control systems, lighting and plumbing fixtures. Exceeding the guarantee, the museum is realizing annual savings of more than $500,000, a 58 percent reduction from the original utility and operating budgets. Humidity fluctuations have been drastically reduced to only 5 percent. In addition, system upgrades have allowed the museum to move from a large to a small service tariff, reducing energy costs more than $30,000 a year. The museum now meets the strict “AA” ASHRAE indoor environment classification requirements and the oftentimes more stringent requirements of art lending institutions and individuals.
“Without the upgrades, many traveling exhibits, including the American Chronicles: The Art of Norman Rockwell and Rembrandt, could not come to the state capital,” says Larry Wheeler, director for the North Carolina Museum of Art. “This tightly controlled museum environment is now protecting priceless collections for generations to come.”
About North Carolina Museum of Art
Maintaining temperature and humidity set points is critical for preserving the North Carolina Museum of Art’s valuable paintings. Replacing ninety-two distributed steam humidifiers, a centralized cold-fog system adds humidity to the dedicated outside air unit.
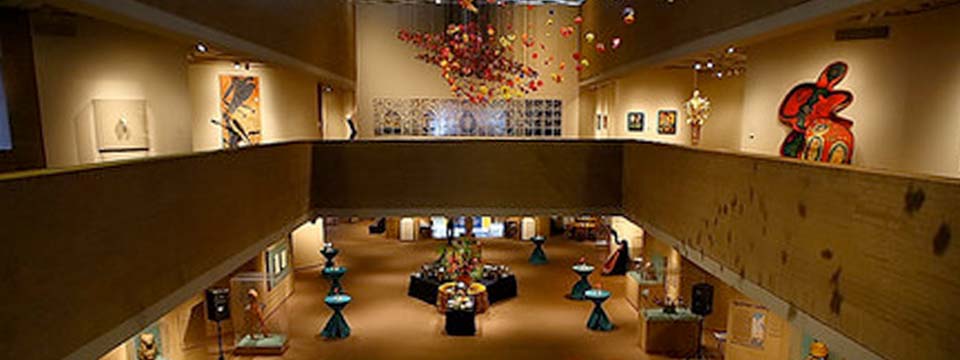