Summary
For more than sixty years, New York City Center has hosted some of America’s, and the world’s, most amazing dance performers and musical theater productions. The entertainment center is a “people’s theater” dedicated to making the arts accessible to the broadest possible audience by creating a welcoming environment, offering subsidized ticket prices and engaging audiences with inspiring programming that reflects the eclecticism, energy and spirit of New York City.
Challenge
In alignment with its mission to enhance the audience and artist experience, New York City Center initiated a comprehensive renovation project to bring back the beauty and charm of its landmark theater. The modernization and restoration plans included a new lighted and heated marquee, plush new seating with expanded leg room and improved sightlines, vibrantly painted decorative wall murals, new carpeting, refurbished dressing rooms and a state-of-the-art sprung stage floor. As part of the renovation, the center was challenged to improve the comfort of its performers on stage, as well as the audience. “We keep the auditorium at about 68 degrees and the stage at about 78 or warmer, which creates a natural convection current," said David Ward, New York City Center, senior director of facilities and capital planning. “In the past, we’ve had some issues with drafts.”
The center sought to upgrade its HVAC systems and controls to improve energy efficiency and reliability, enhance air quality and increase comfort. Not wanting to lose a performance season, the project needed to adhere to a tight schedule, working around already booked shows.
Solution
Building owners assembled a team of experts, including Ennead Architects; engineering firm, Cosentini Associates; general contractor, F.J. Sciame Construction Company; mechanical contractor, Knoller Company; and Trane, a world leader in HVAC systems and services. The group worked together to design and execute the renovation, with Trane providing guidance and assistance with equipment and controls. A schedule was developed, with the work planned in two phases to ensure minimal disruption to the business.
Reducing energy consumption
A smaller, 100-ton chiller was added to work along with two previously installed 360-ton Trane CenTraVac™ chillers. To reduce energy consumption the new, smaller chiller is used for minimum consumption events, such as performances in the center’s small theaters. The larger chillers are used on hot days and during full-house, main-stage productions.
Controlling costs, ensuring comfort
Trane temperature and humidity sensors were installed to control operating mode set points to meet appropriate levels based on occupancy. Carbon dioxide sensors were added to existing Trane air handling units throughout the theater to optimize the amount of fresh air brought in for improved air quality and safety. Variable frequency drives control pump speed to reduce energy use, extend motor life and maximize occupant comfort.
The theater’s existing Trane Tracer Summit® building automation system (BAS) was upgraded to expand the capacity and control of the theater’s HVAC systems to maximize building performance. The BAS allows the operator to monitor and control equipment to increase energy efficiency and enables the building engineer to switch back and forth between the large and small chillers, depending on consumption needs. Building owners employ chiller tower optimization through the use of the Trane Tracer Summit Chiller Plant Manager system, sequencing chiller set points to reduce energy consumption. The BAS allows the center to take advantage of airside control strategies to adjust airflow for occupancy levels.
“Audiences want to have it cool and dancers want it very warm for their muscles,” said Ward. “Of course the auditorium and stage are connected, but nonetheless we try to control them as if they were completely separate rooms. We’ve largely been able to overcome problems by adjusting fan speeds and air supply, so it almost creates an air curtain. We have so many different requirements, but once we set up basic parameters for a particular performance type and audience size, the BAS runs automatically.”
Results
Renovations at the New York City Center have restored the beauty of the historic theater and created a healthier, more energy efficient environment. The improvements have resulted in an estimated annual energy savings of 6,489 million BTUs and have helped to achieve a Silver LEED (Leadership in Energy and Environmental Design) rating. LEED is the nationally accepted benchmark for the design, construction and operation of high-performance, environmentally conscious buildings.
The dancers performing on stage and the patrons viewing the shows are now both more comfortable. New York City Center is pleased to welcome upcoming events to its renovated venue, including the return of the New York City Opera Company, which had its start there in the 1940s.
“In the past year, we have had almost zero performer and audience complaints,” said Ward. “It’s pretty amazing. No more drafts!”
About New York City Center
New York City Center includes a 2,257-seat auditorium, two small theaters, four rehearsal studios and a twelve-story office tower.
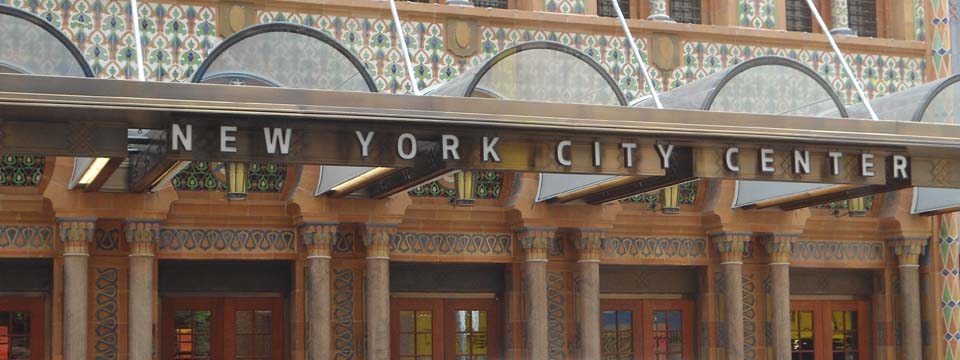