Project Highlights
Location: Vancouver, British Columbia, CA
Industry: Commercial Real Estate
Products Used: Chillers, Energy Storage,
Services Used: Energy Analysis & Monitoring, Start-up Maintenance, Upgrading,
Climate: Humid & Cold
Topic: Sustainability, Efficiency, Cost-Saving, Optimal Comfort, Thermal,
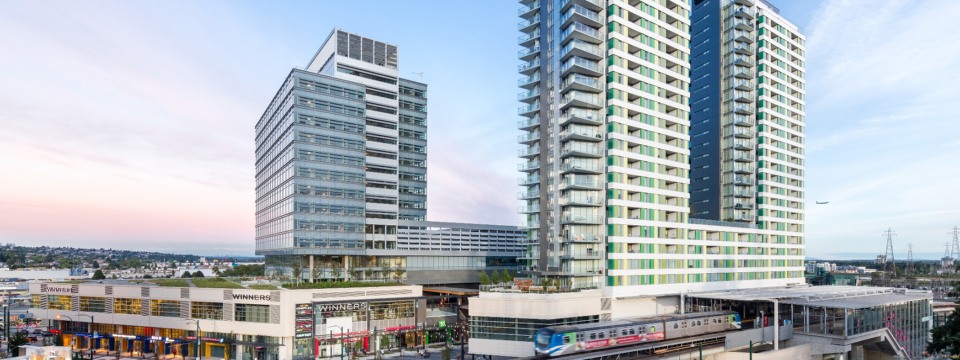
Challenge
Rather than having each building of the large, all-new-construction Marine Gateway development run its own furnaces, boilers and chillers, it was determined that a district energy plant would offer a more efficient way to provide heating and cooling for the property and also enable energy sharing with surrounding buildings should there be an opportunity. With the district energy plant, property developer PCI Developments sought to address the simultaneous heating and cooling needs of the mixed-use property, as well as align with the renewable energy requirements of the city by reducing the development’s carbon footprint.
Solution
PCI Developments contacted thermal energy utility owner and operator FortisBC Alternative Energy Services (FAES) to discuss their district energy plant needs. FAES owns twenty-seven operating projects across forty-five sites in BC, providing service to nearly seven million square feet, which constitutes approximately 60,000 MWh of thermal energy per year. The utility company also provides 24/7 emergency service to its customers. FAES managed design and construction of the project, and engaged with Pinchin Ltd, one of Canada’s largest environmental, engineering, health and safety consulting firms, to conduct a feasibility study and detailed design for the district energy system. Pinchin consulted with Trane regarding the plant design based on Trane’s district energy center and heat recovery systems knowledge, as well as the company’s cradle to grave capabilities.
The multi-entity project team worked together to develop a low carbon energy system (LCES) incorporating geoexchange and energy sharing to maximize the level of renewable thermal energy delivered to the residential, commercial, and retail customers in the development. The engineering consultant calculated the maximum and minimum heating and cooling loads for the mixed-use development. Working with Trane, energy modeling was performed to establish optimal sizing and select equipment that would meet performance and energy objectives.
Answering heating and cooling needs with greater efficiency
The mixture of residential, retail, and commercial occupancies led to substantial concurrent heating and cooling loads. Pinchin proposed a geoexchange and heat-recovery based district energy system for this site. The energy center includes 400 tons of dedicated heat recovery chillers (DHRCs), supplied by Trane, which provide simultaneous heated water to the entire development and chilled water to the office tower and retail units. Trane also supplied the other major equipment for the energy center including four high-efficiency condensing boilers, two Trane® Optimus™ water-cooled chillers (Model RTHD), and six plate and frame water-to- water heat exchangers.
Ensuring comfort, reducing gas consumption
With a semi-hermetic design and helical rotary technology, the two energy efficient Trane® Optimus™ chillers provide dependable operation to keep tenants and residents of the office tower and retail units cool during summer months. Excellent compressor life and continuous unloading help ensure efficiency for high-occupancy buildings in the development.
In order to capture renewable energy, the fourteen dedicated heat recovery chillers take heat typically rejected by the cooling system and reuse it to heat the buildings and supply domestic hot water. Using heat recovery helps to improve building efficiency, and reduces input energy and fuel costs.
Employing a renewable energy source
The district energy plant includes a geoexchange bore field to meet project low energy use and low carbon objectives. Glycol inside the ground loop is circulated through over 300 vertical closed-loop boreholes. In the winter, the DHRCs extract heat from the ground loop and provide heating water for the buildings. In the summer, heat from cooling is rejected to the ground loop to be used until the winter months.
Maintaining optimal performance
Trane factory-authorized professional technicians provide service and ongoing maintenance to FAES as the owner and operator of the system to keep the district energy plant running at its best, helping to ensure system performance and reliability, as well as comfort for Marine Gateway tenants. The Trane service and maintenance contract also allows the facility to address maintenance needs on a scheduled basis rather than reacting to urgent service needs and emergency repairs.
Results
Demonstrating the company’s cradle to grave capabilities, Trane provided guidance during initial plant design, equipment selection and installation as well as ongoing service and maintenance of the equipment. The low carbon energy system is helping the development to provide comfort for tenants, lower energy use and reach carbon footprint reduction goals. The energy efficient, sustainable district energy plant design helped the Marine Gateway development to achieve LEED Gold® certification.
“The district energy plant has been in operation for more than two years and the performance has been outstanding,” said Andrew Byrnes, P.Eng. and project manager for Pinchin Ltd. “We’re very proud of the results. We’ve exceeded our rather substantial target of using 70 percent renewable energy.”