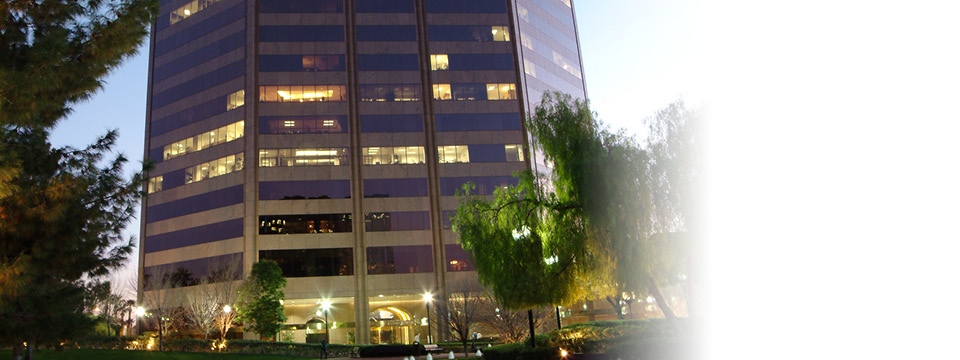
Challenge
To serve a tenant population comparable to the size of a small city, building owner McCarthy Cook & Co was paying electric bills in excess of $700,000 a year at its Central Arts Plaza tower. The company sought to reduce operational costs and better manage energy use in the facility by replacing obsolete and difficult to maintain systems.
Solution
The Central Arts Plaza operations manager discussed reducing overhead costs with Trane, the building’s HVAC equipment and service contractor since its construction. With new Trane technologies developed over the years that would answer the building owner's efficiency objectives, energy rebates offered by the local utility company, and incentives available from the City of Phoenix through the Energize Phoenix program, the team determined that it was the right time to move forward with the upgrade.
McCarthy Cook & Co and Trane reviewed budget proposals, identified energy conservation measures (ECMs) that would reduce operational costs, and using TRACE™ 700, evaluated each ECM. The energy saving improvements identified as having the greatest impact were updating the building's aging Energy Management System (EMS) and Central Plant Manager Control System, and adding Trane® Adaptive Frequency™ Drives (AFDs) to the central plant chillers.
Enabling strategic decision-making
Central Arts Plaza uses a multitude of Trane® Intelligent Services to manage energy use. Energy Performance, a cloud-based dashboard, tracks and optimizes building performance using advanced energy analytics and visualization tools to transform data into actionable recommendations, uncover areas of energy waste and enable informed decisions to trim energy costs. An Energy Assessment using Energy Analyzer employs pulse meters to provide building managers with a real time view of utility use, as well as comparisons to historical consumption data. During quarterly review meetings, Trane and building operators assess energy use and make adjustments as needed to enhance savings.
Improving energy efficiency
Without disturbing tenants in the fully-occupied building, a central plant retrofi t was completed to help reduce the building’s peak demand and the need to run multiple chillers. The nearly thirty year old chillers in the plant were rebuilt and upgraded with Trane Adaptive Frequency™ Drives (AFDs). The AFDs maximize chiller efficiency and reduce power consumption by adapting the compressor motor speed and inlet guide vanes to the chiller operating temperatures. The large, 12-inch touch screen of the Tracer AdaptiView™ chiller controls instantly conveys at-a-glance feedback on status and alarms, with detailed reports and graphs presenting easily understandable data for documenting and optimizing energy efficiency. The underlying intelligence of AdaptiView™ is the Adaptive Control™ algorithms that include patented strategies to respond to normal or extreme conditions to maintain effective chiller plant operation.
Optimizing system performance
Tracer™ ES, a web-based systems integration solution, gives facility managers an online view of the building systems from any PC or mobile device on the network. The user-friendly Tracer™ ES enables building managers to perform daily operations, such as scheduling, making set point changes, and conducting data analysis for better decision-making. The Tracer Chiller Plant Control application precisely matches capacity to cooling load to optimize chiller plant energy efficiency; displays operating conditions on status screens for easy viewing; provides alarm and diagnostic messages; and enables easier monitoring and troubleshooting.
Results
A strong collaboration between McCarthy Cook & Co and Trane to implement energy saving measures, including Trane Energy Performance, Energy Assessment, AFDs and Tracer™ ES, has resulted in significant savings at the Central Arts Plaza. Year-over-year electric demand data shows a drop in daily demand of more than 1,000 KW a day, a savings of more than $200,000 annually. Project timing allowed the building owner to leverage City of Phoenix incentives and utility company rebates in excess of $380,000. Moving from an average of twenty-five hot/cold calls a day to just one, facility managers are now able to spend more time focusing on customer service.
“Our twenty-six year old rebuilt chillers are performing like brand new,” said Ron Lloyd, operations manager, McCarthy Cook & Co. “The Energy Management System is easy to use, the drives hit it out of the park, and the central plant controls married the two together. Adding capital to our building has definitely increased its value.”
Trane, the Circle Logo, TRACE, Adaptive Frequency, AdaptiView, Adaptive Control, and Tracer are trademarks of Trane in the United States and other countries.
Challenge
To serve a tenant population comparable to the size of a small city, building owner McCarthy Cook & Co was paying electric bills in excess of $700,000 a year at its Central Arts Plaza tower. The company sought to reduce operational costs and better manage energy use in the facility by replacing obsolete and difficult to maintain systems.
Solution
The Central Arts Plaza operations manager discussed reducing overhead costs with Trane, the building’s HVAC equipment and service contractor since its construction. With new Trane technologies developed over the years that would answer the building owner's efficiency objectives, energy rebates offered by the local utility company, and incentives available from the City of Phoenix through the Energize Phoenix program, the team determined that it was the right time to move forward with the upgrade.
McCarthy Cook & Co and Trane reviewed budget proposals, identified energy conservation measures (ECMs) that would reduce operational costs, and using TRACE™ 700, evaluated each ECM. The energy saving improvements identified as having the greatest impact were updating the building's aging Energy Management System (EMS) and Central Plant Manager Control System, and adding Trane® Adaptive Frequency™ Drives (AFDs) to the central plant chillers.
Enabling strategic decision-making
Central Arts Plaza uses a multitude of Trane® Intelligent Services, part of the Trane® Building Advantage™ portfolio, to manage energy use. Energy Performance, a cloud-based dashboard, tracks and optimizes building performance using advanced energy analytics and visualization tools to transform data into actionable recommendations, uncover areas of energy waste and enable informed decisions to trim energy costs. An Energy Assessment using Energy Analyzer employs pulse meters to provide building managers with a real time view of utility use, as well as comparisons to historical consumption data. During quarterly review meetings, Trane and building operators assess energy use and make adjustments as needed to enhance savings.
Improving energy efficiency
Without disturbing tenants in the fully-occupied building, a central plant retrofi t was completed to help reduce the building’s peak demand and the need to run multiple chillers. The nearly thirty year old chillers in the plant were rebuilt and upgraded with Trane Adaptive Frequency™ Drives (AFDs). The AFDs maximize chiller efficiency and reduce power consumption by adapting the compressor motor speed and inlet guide vanes to the chiller operating temperatures. The large, 12-inch touch screen of the Tracer AdaptiView™ chiller controls instantly conveys at-a-glance feedback on status and alarms, with detailed reports and graphs presenting easily understandable data for documenting and optimizing energy efficiency. The underlying intelligence of AdaptiView™ is the Adaptive Control™ algorithms that include patented strategies to respond to normal or extreme conditions to maintain effective chiller plant operation.
Optimizing system performance
Tracer™ ES, a web-based systems integration solution, gives facility managers an online view of the building systems from any PC or mobile device on the network. The user-friendly Tracer™ ES enables building managers to perform daily operations, such as scheduling, making set point changes, and conducting data analysis for better decision-making. The Tracer Chiller Plant Control application precisely matches capacity to cooling load to optimize chiller plant energy efficiency; displays operating conditions on status screens for easy viewing; provides alarm and diagnostic messages; and enables easier monitoring and troubleshooting.
Results
A strong collaboration between McCarthy Cook & Co and Trane to implement energy saving measures, including Trane Energy Performance, Energy Assessment, AFDs and Tracer™ ES, has resulted in significant savings at the Central Arts Plaza. Year-over-year electric demand data shows a drop in daily demand of more than 1,000 KW a day, a savings of more than $200,000 annually. Project timing allowed the building owner to leverage City of Phoenix incentives and utility company rebates in excess of $380,000. Moving from an average of twenty-five hot/cold calls a day to just one, facility managers are now able to spend more time focusing on customer service.
“Our twenty-six year old rebuilt chillers are performing like brand new,” said Ron Lloyd, operations manager, McCarthy Cook & Co. “The Energy Management System is easy to use, the drives hit it out of the park, and the central plant controls married the two together. Adding capital to our building has definitely increased its value.”