Life Science facilities require a unique environment with highly specific temperatures, humidities, and pressures. And for good reason. Tight environmental controls mean predictable quality. Manufacturing the world’s pharmaceuticals relies on precision, predictability, and repeated excellence. Because of this, it is one of the most highly regulated industries and subject to regular audits. Life Science manufacturers need reliable systems to track, store, and protect their building automation system data to help ensure 21 CFR Part 11 compliance and simplify the audit process.
Trane's Tracer® Ensemble® building management system, with the Critical Control, is designed to give manufacturers in highly regulated industries the tools needed to track and store their facility data. Designed to manage a facility's environment, from temperature, humidity, pressure, and lighting, the system’s SQL database server functions as a data historian that maintains critical system data to streamline operations, meet the requirements of 21 CFR Part 11, and ensure simple, routine compliance.
3 Benefits of Digitized Recordkeeping
Facility management plays a fundamental role in the development and manufacture of repeatable and effective drug products. Temperature, humidity, and pressure data is also one of the easiest things to digitize, bringing simplicity to compliance, engineering investigations, and quality management. Sound data management procedures can help support compliance, as well as assist engineering in implementing more efficient, reliable systems.
- Build Efficiency
Digital tracking can help eliminate time-consuming and redundant paper processes. It keeps employees focused on higher-value tasks while maintaining proper records to help ensure compliance. By using an integrated building management system, you can remotely access, monitor, and manage your operation while also automating compliance via audit trail. This helps to cut down on costly human errors, catch problems before they become a crisis, and streamlines operations.
Tip: Find a building management system that’s flexible enough to work with applicable security measures and that complies with SOPs.
- Streamline Compliance
Audits are a regular part of Life Science operations. Whether it’s coming from the FDA or another regulatory entity, this cumbersome and time-consuming task can be streamlined with organized, digital facility data. Version control is simplified since an electronic document can track every change, including date and time stamps, as well as personnel details about who made the change.
Having this level of detailed data at your fingertips eases audit prep, ensures accuracy, and supports quick root cause analysis in the event of a failure.
- Risk Mitigation
When backed up correctly, digital records can help to provide an added layer of security to your operations. Digital records provide the ability to easily manage access controls and clearance levels. Using redundant storage methods means that your critical data are backed up to a remote location that can be accessed during a disaster recovery event.
Tracer® Ensemble®: Designed for Compliance
21 CFR Part 11 outlines specific system requirements for recordkeeping and recording. The following outlines how using Tracer® Ensemble® with Critical Control can digitize recordkeeping to bring important security and efficiency to Life Science operations.
Electronic Signatures
Electronic signatures are the electronic equivalent of a person’s actual signature and are considered legally binding. 21 CFR Part 11 and the subsequent guidance document define the criteria for when an electronic signature is required and how that signature should be qualified so that it is considered equivalent to a handwritten signature. Both technical implementation of the electronic signatures and procedural level controls characterize the proper use of electronic signatures.
The Tracer® Ensemble® control system has a dual token (username and password) login along with rigorous user security to maintain data integrity. Electronic signatures are protected against unauthorized changes, are linked to the respective documents to avoid transfer, and the signed records are protected to prevent changes after execution.
Electronic Records
Electronic records are pieces of data, stored electronically, that are used to satisfy compliance requirements. This may include data used to report on system performance, product quality, and more. 21 CFR Part 11 provides the framework for classifying electronic records and specifies the need to define a secure environment to guarantee the integrity of these records.
The Tracer® Ensemble® control system ensures data integrity by using Microsoft SQL database technology to store system files, audit trail data, system alarms, and critical environmental trend data. Standard or custom reports can be generated by date range and exported in a variety of formats. Reports can include user change logs, data logs, alarm logs, and override reports. Each application can be configured to store data for a specific time period or indefinitely.
Audit Trail
The audit trail tracks an operator’s actions to ensure system integrity. The supervisory control system must generate a secure time-stamped audit trail that independently records the date and time of operator actions that create, modify, or delete high-impact (GxP) electronic records. The audit trail shall be made at the time the action/operation is conducted electronically.
The Tracer® Ensemble® control system tracks alarms and daily operator activities and stores them as electronic records in a secure audit trail. Audit trail functionality is always-on, time-controlled, and protected from unauthorized change. It can be easily exported to be archived and shared with third parties.
System Security
21 CFR Part 11 details requirements related to system access, retention periods, and identity verification. Limiting access to authorized individuals and having robust guardrails in place ensures system security and data integrity.
The Tracer® Ensemble® control system includes robust security protocols, including password rules, to ensure appropriate user permissions, system validation procedures, security system configuration for individual user roles, and application backup and archival functionality.
Finding the Right Vendor
As you make the move from paper to digital reporting, it’s important to find a vendor who can best support your reporting needs as well as the entire mechanical system operations. Having a single point of contact who can both optimize your mechanical systems and ensure appropriate compliance will bring important efficiencies to your business.
An integrated building management system built for compliance.
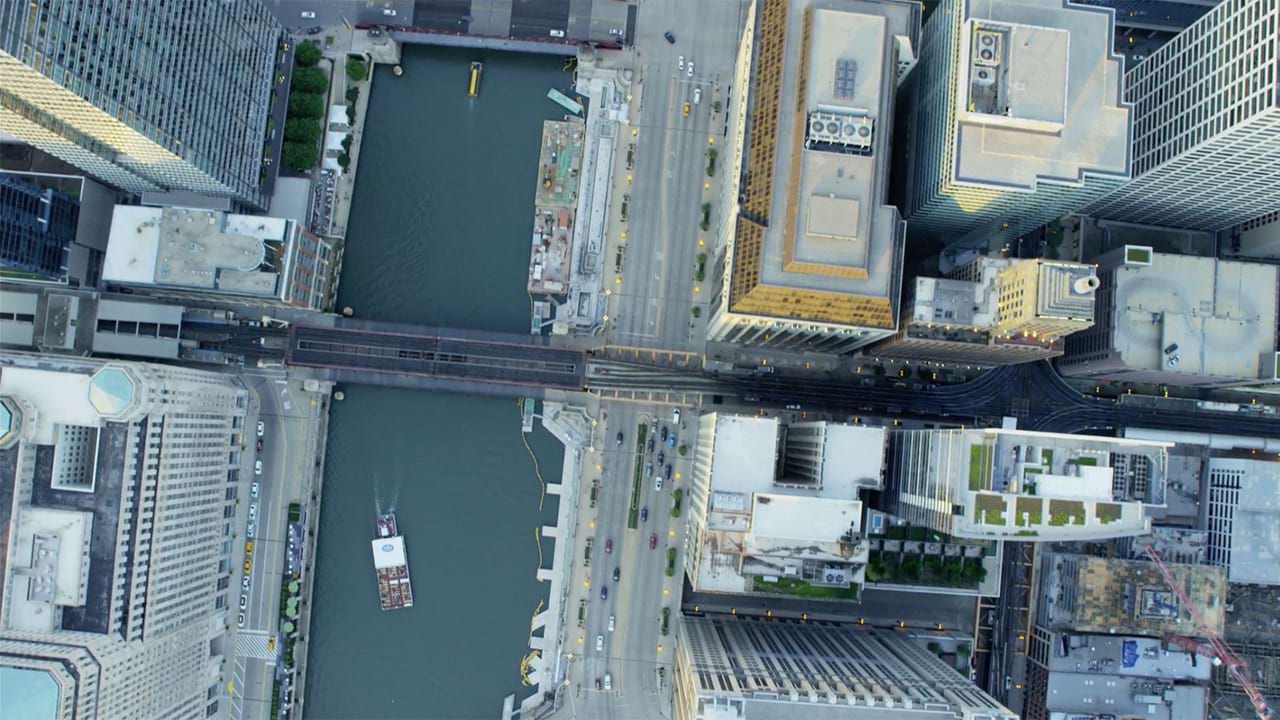
Trane is dedicated to helping you meet decarbonization efforts efficiently while being cost-effective.
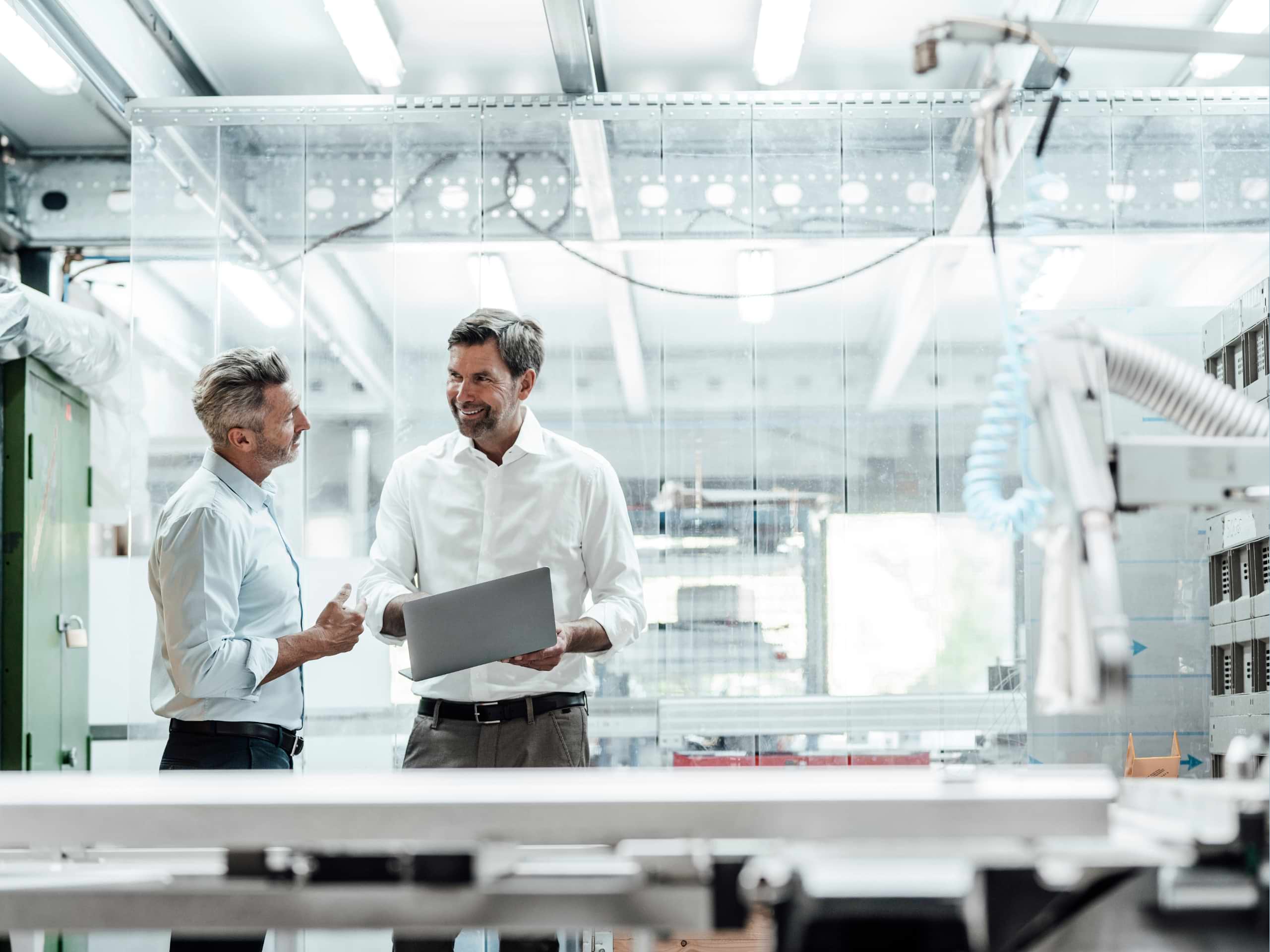
In the high tech manufacturing industry, even the smallest deviation from the required environmental conditions can have a significant negative impact on product quality. Therefore, precision control and quality management are of utmost importance.
-
Blog
-
Connected Buildings
-
Life Sciences
-
Building Automation
-
Achieve Building Decarbonization With Modern Controls
Trane is dedicated to helping you meet decarbonization efforts efficiently while being cost-effective.
-
No Margin for Error: Four Ways Precision HVAC Impacts Your High Tech Manufacturing Facility
In the high tech manufacturing industry, even the smallest deviation from the required environmental conditions can have a significant negative impact on product quality. Therefore, precision control and quality management are of utmost importance.
-
How to Maintain Constantly Evolving Smart Buildings
Modern building systems must support devices from yesterday, today, and tomorrow. Here are some best practices for how to make that all work.